Quality Control
Achieving Excellent Quality Management Through Advanced Equipment
Our commitment to quality starts with state-of-the-art equipment. Through a series of advanced equipment to inspect the physical and chemical properties of materials and detect possible defects or anomalies, we ensure that all castings meet the most stringent standards and specifications to achieve excellent quality management and control.
We use the following quality control equipment:
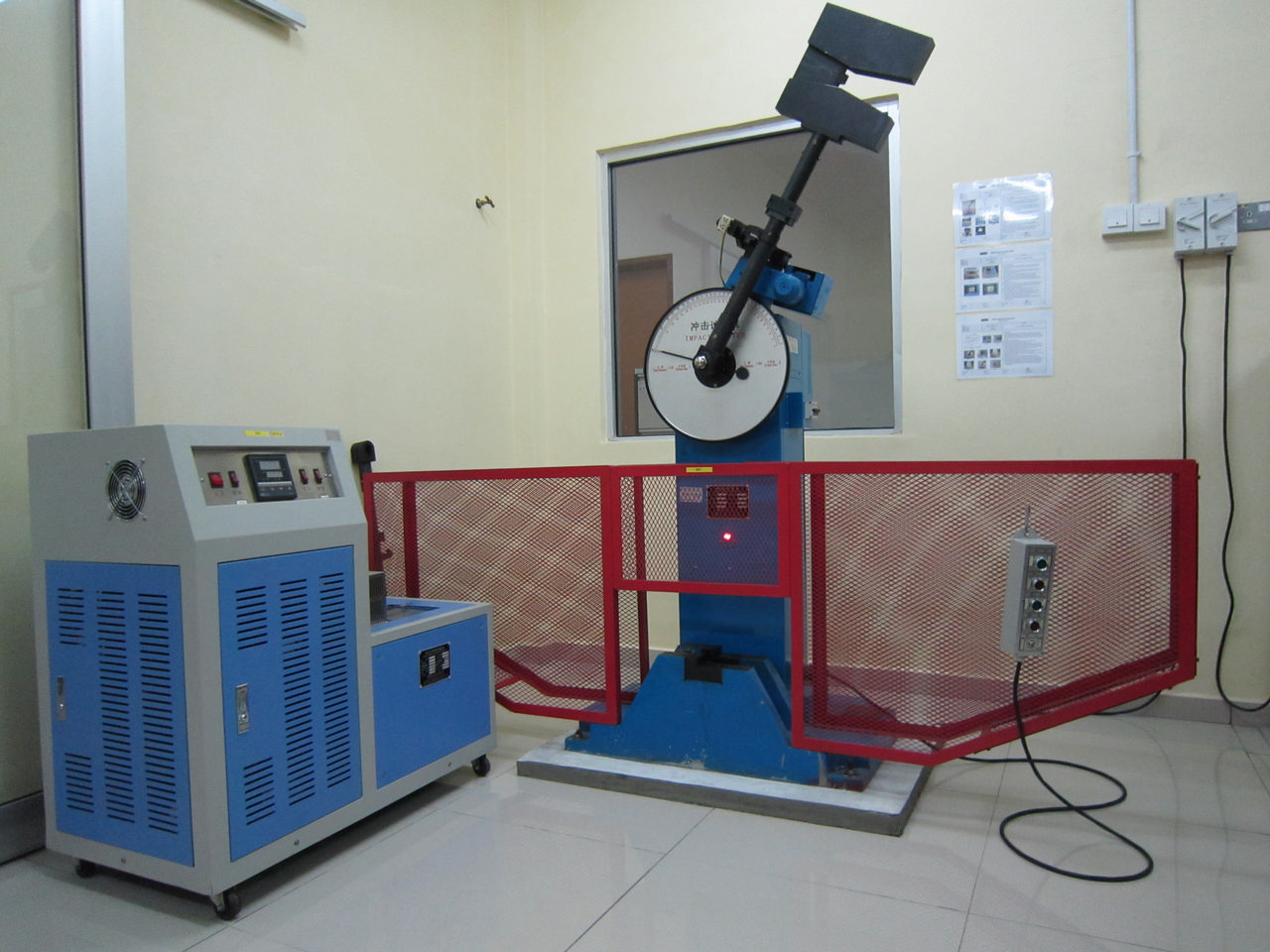
Charpy impact tester
to measure the required toughness of a metal piece

Magnetic particle flaw detector
to check surface cracks or sub-surface defect
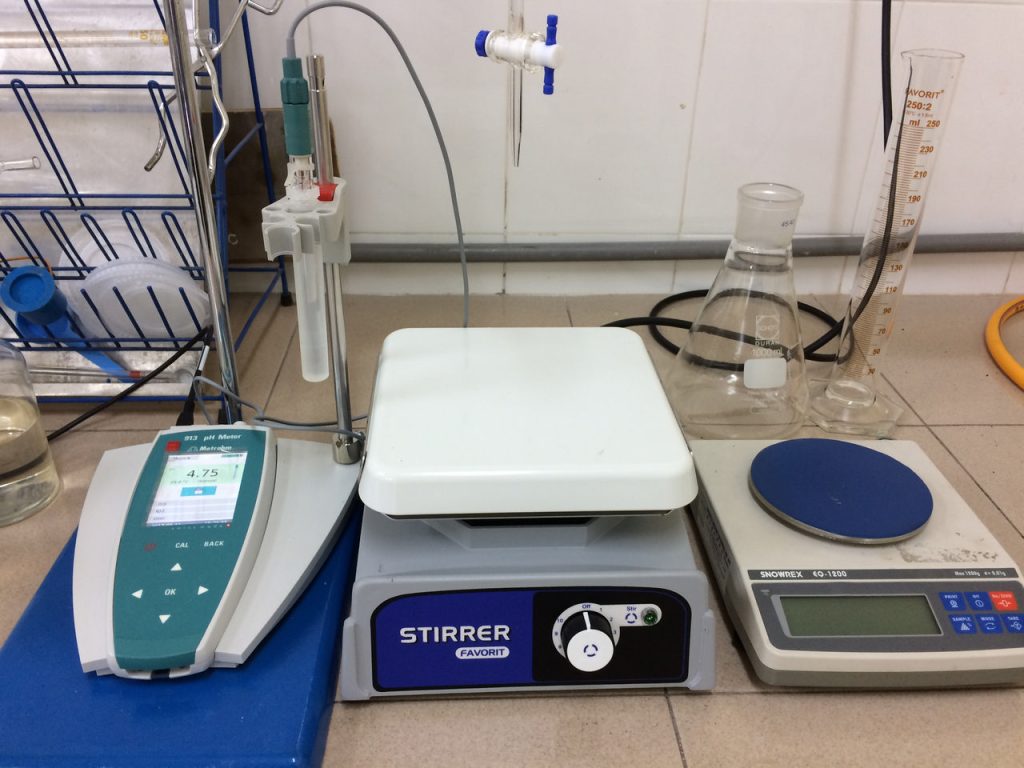
pH Meter
to check the ADV and pH value of moulding sand
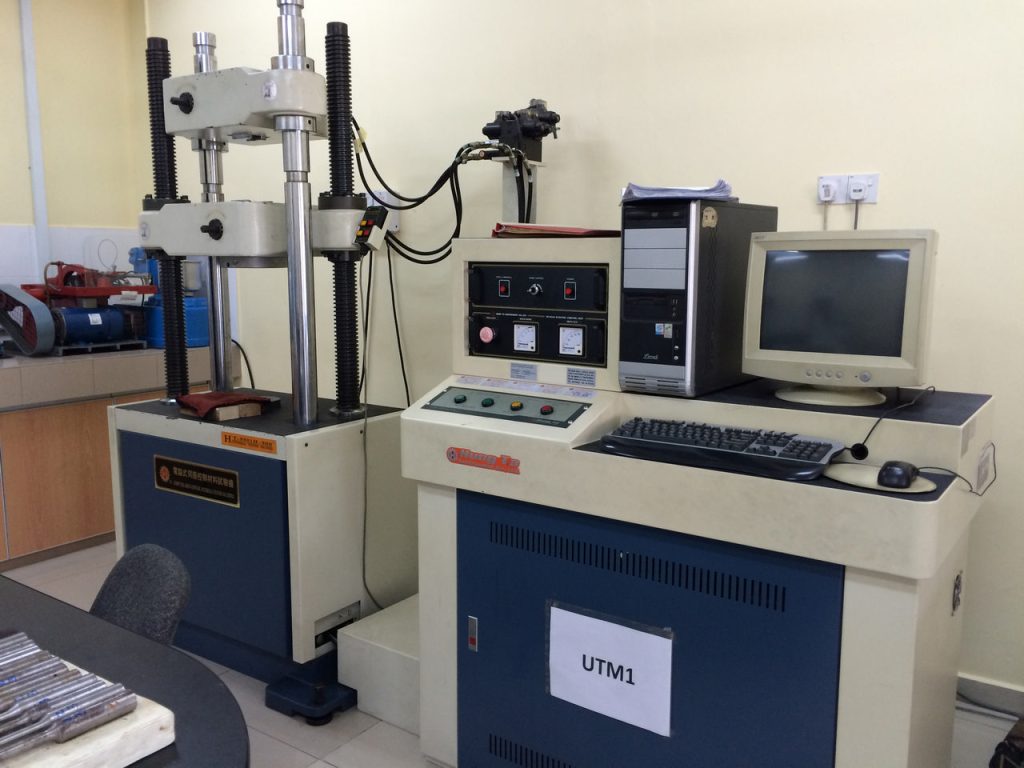
Universal testing machine
to test the tensile strength, compressive strength, bending properties of metal
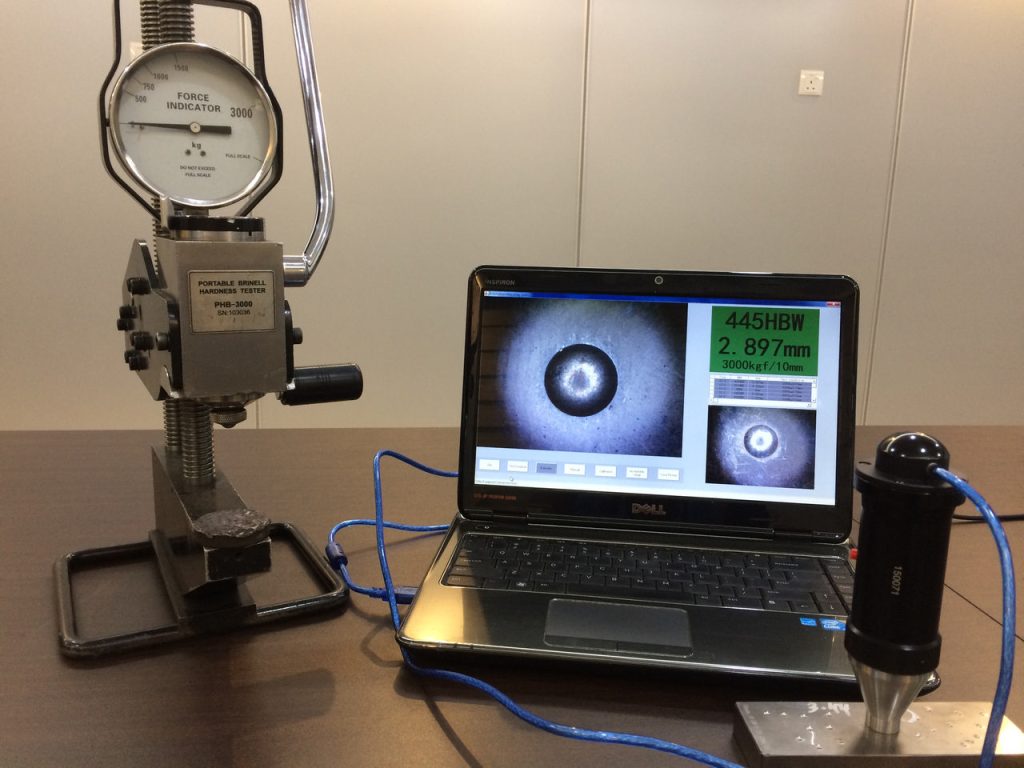
Hardness tester
to check the hardness of a casting

Sand sieve analyser
to determine the grain size distribution of sand
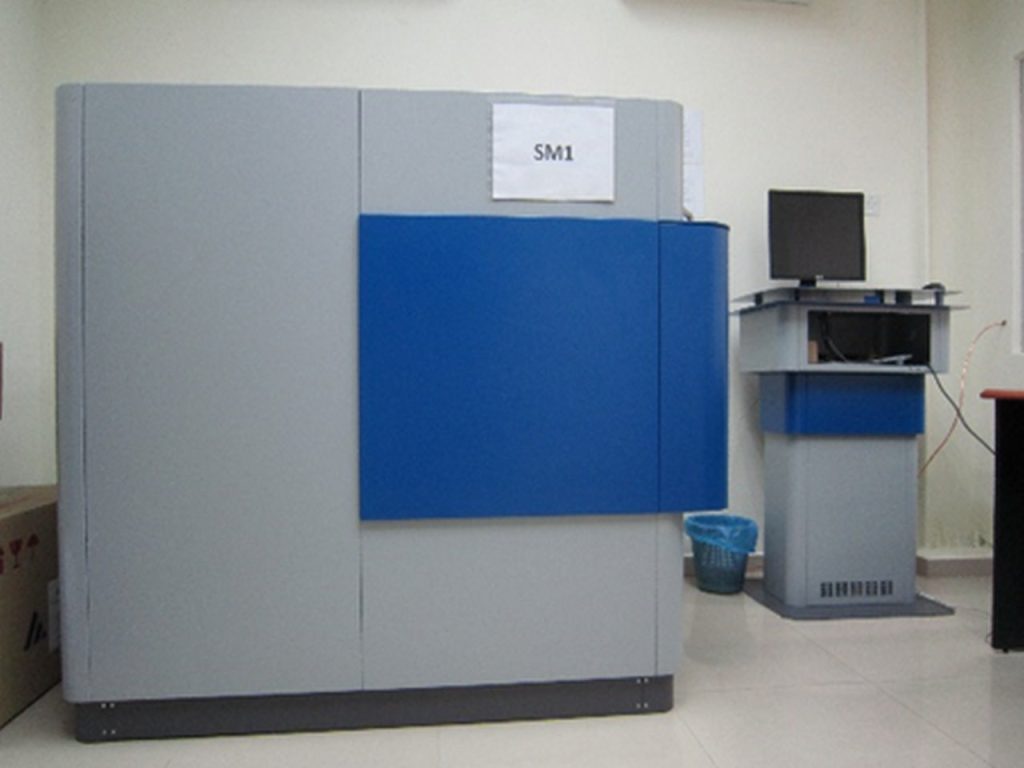
Spectrometer
to check the chemical composition of metal
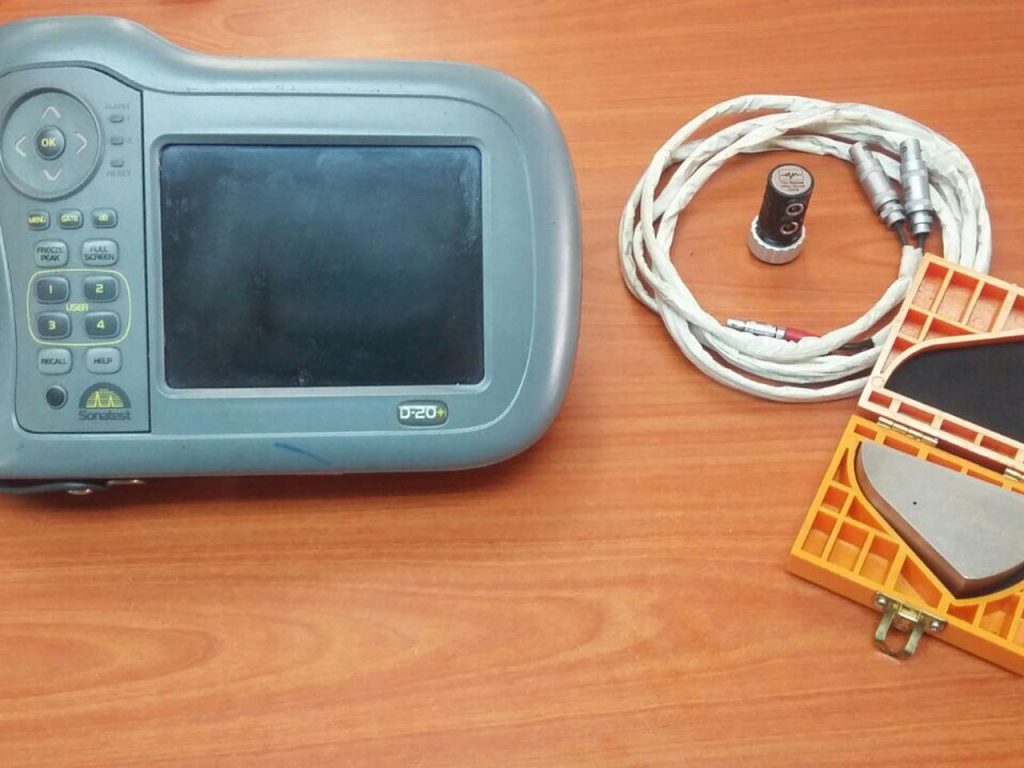
Ultrasonic flaw detector
to look for internal defects in casting
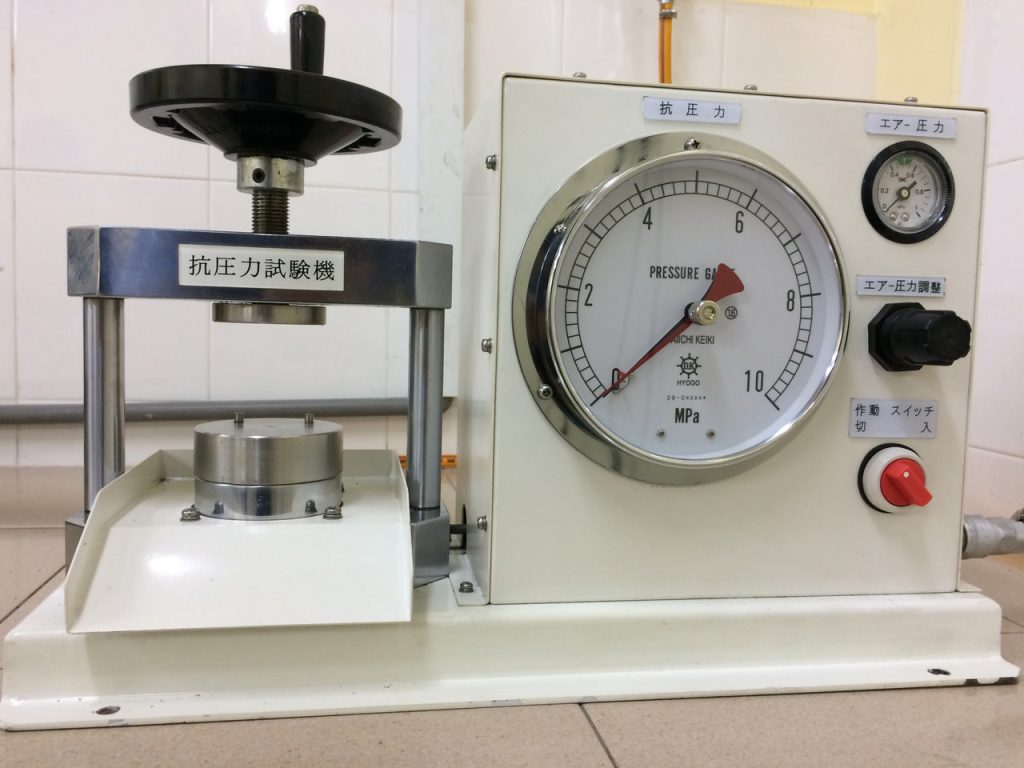
Sand Compressive Strength Tester
to check the compressive strength of resin-bonded moulding sand
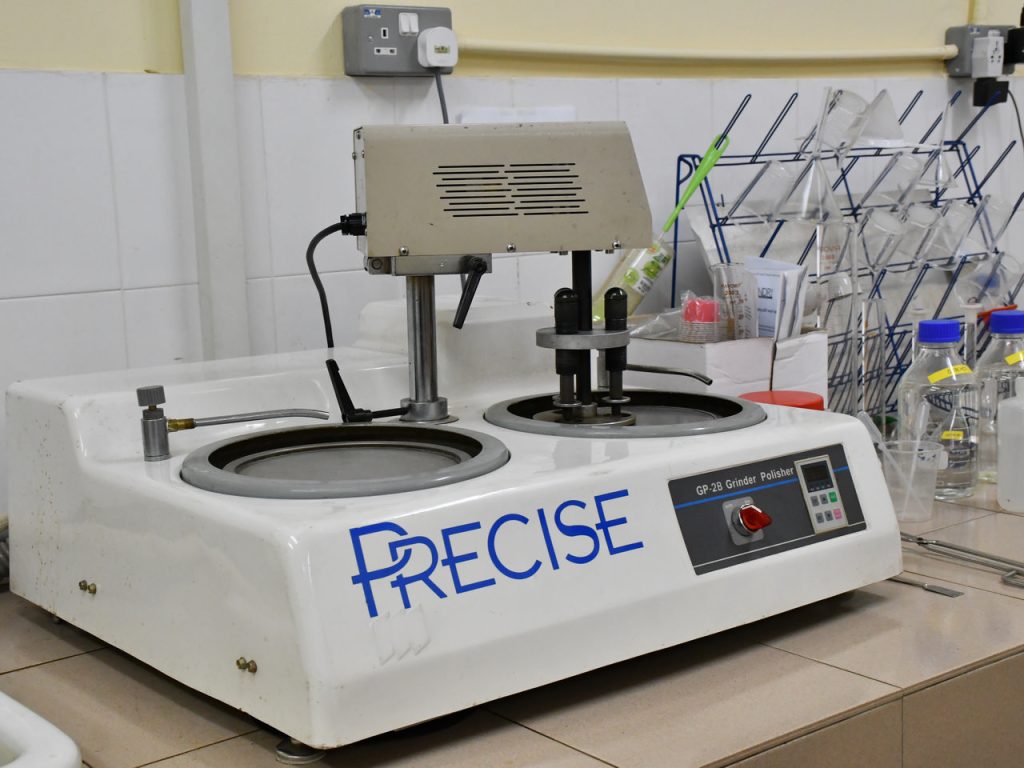
Specimen grinder/polisher
to grind and polish metal samples for microstructure examination
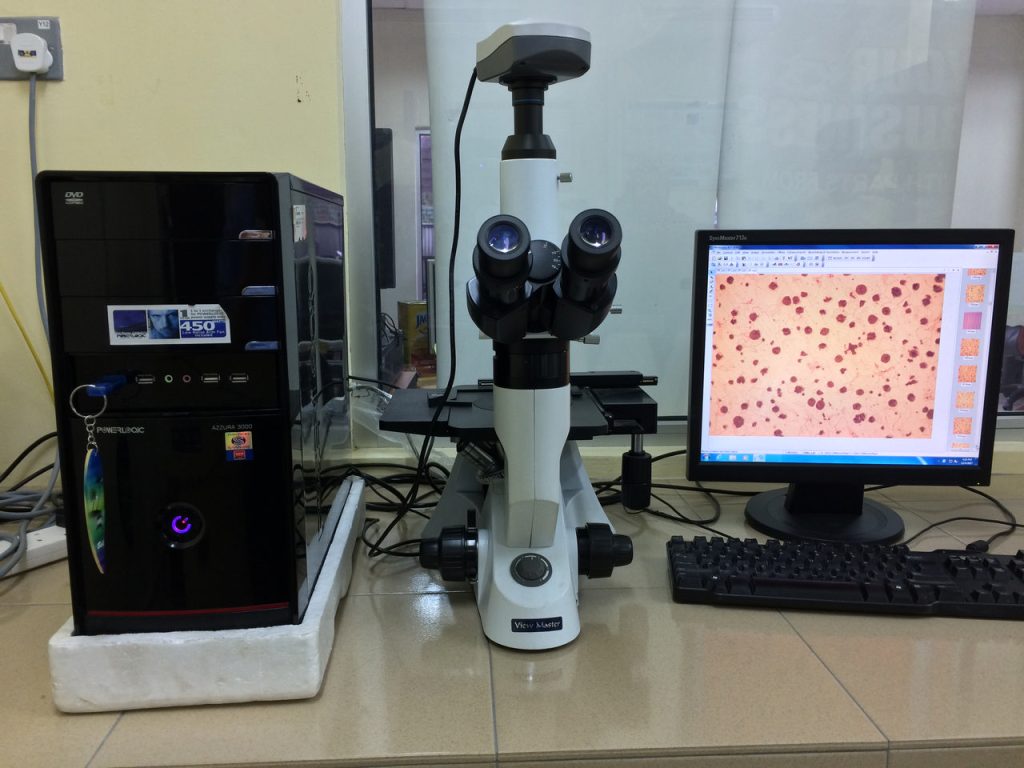
Metallurgical microscope
to examine the microstructure of metal
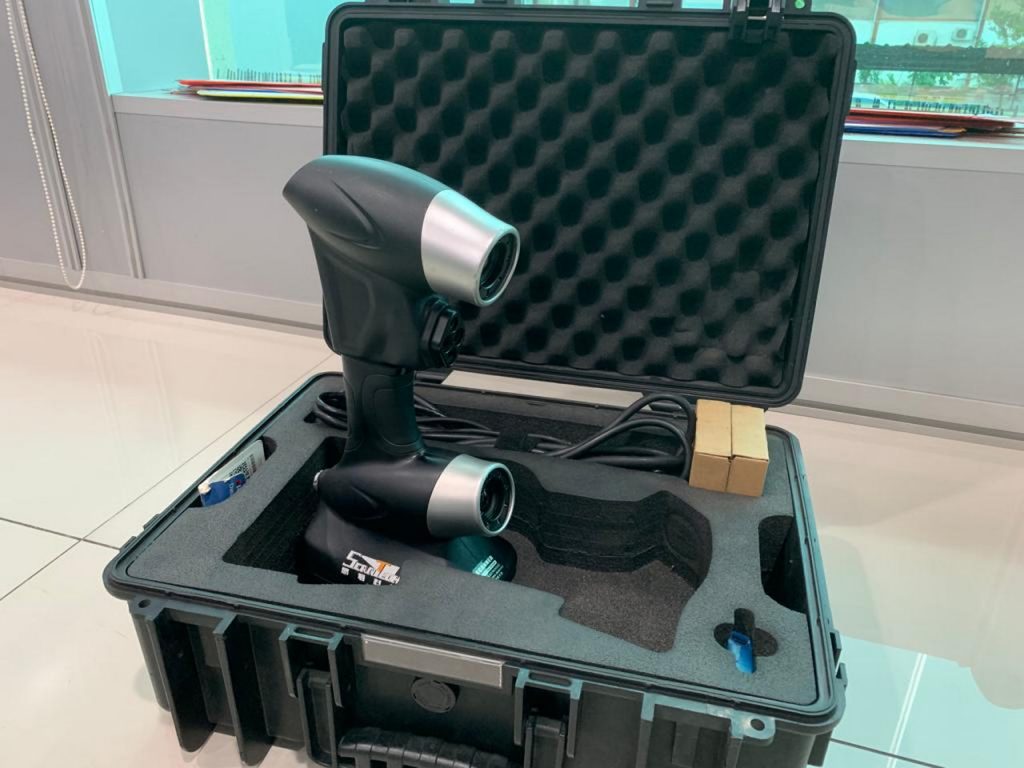
3D scanner
to check and determine the dimensions of a casting
State-of-the-art Software
Advanced Leading Software Optimizes Production Processes & Enhances Casting Quality
Committed to providing the highest quality casting products, we exclusively use industry-leading professional software, including Magmasoft, Novacast, and FRP to continuously enhance our production and process control.
These software applications are world-leading products explicitly developed for the foundry industry. We can more accurately predict and optimize casting quality through advanced technology, ensure high production process efficiency, shorten delivery time, and offer customers exceptional castings.
The following account depicts the advantages of using this software:
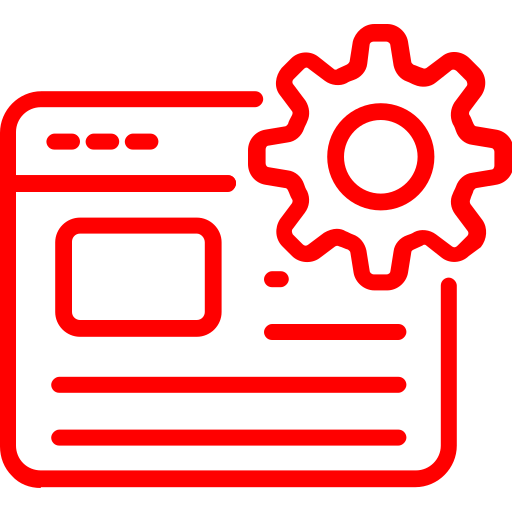
Determine parameters that have a significant impact on casting defects
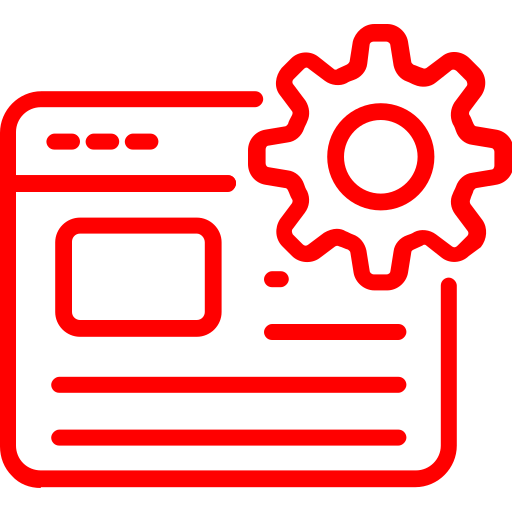
Identify a reliable gating and risering system to produce acceptable casting quality
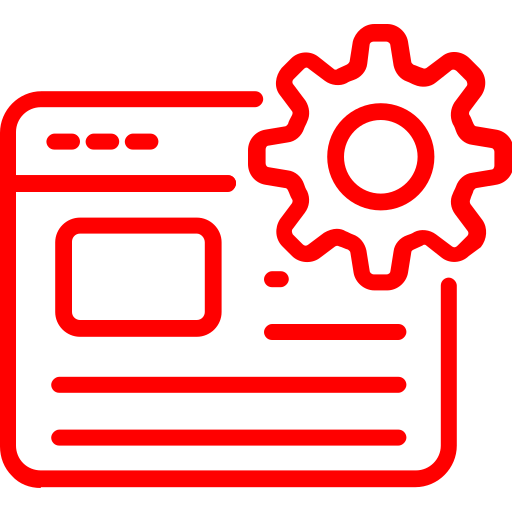
Able to stimulate various kinds of materials (in detail) in casting simulation
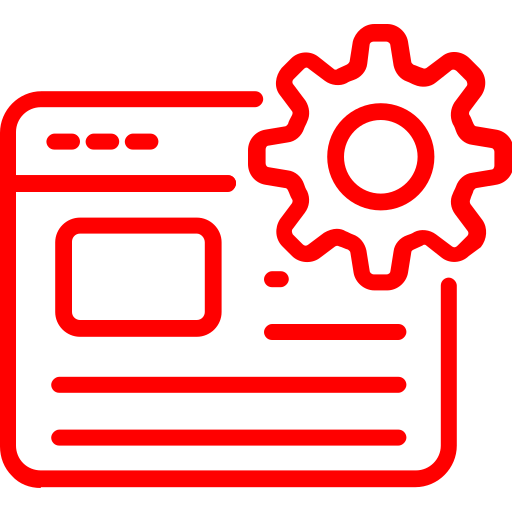
Improve casting productivity (shorten lead time)
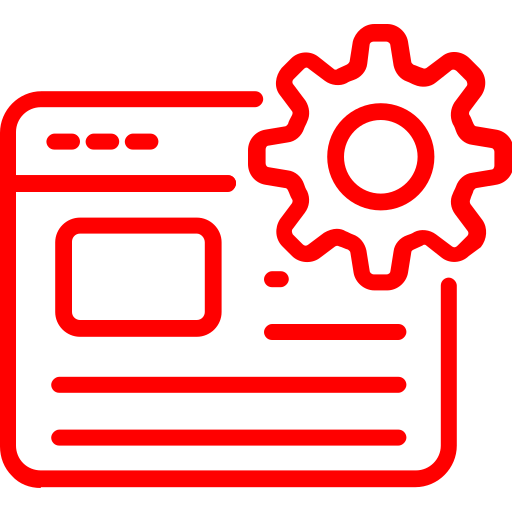
Enhance the planning and traceability of casting production
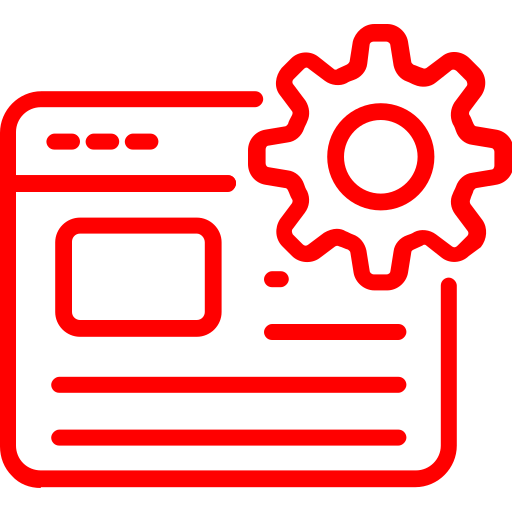
Reliable and leading software branding in the foundry industry
Quality Inspection
Stringent Quality Inspection Measures for Superior Castings
Our casting process principle centres around the pursuit of excellence. To this end, we implement a series of rigorous quality inspection measures to ensure that casting quality and performance meet customer’s standards. Appended below is a series of quality inspection measures:
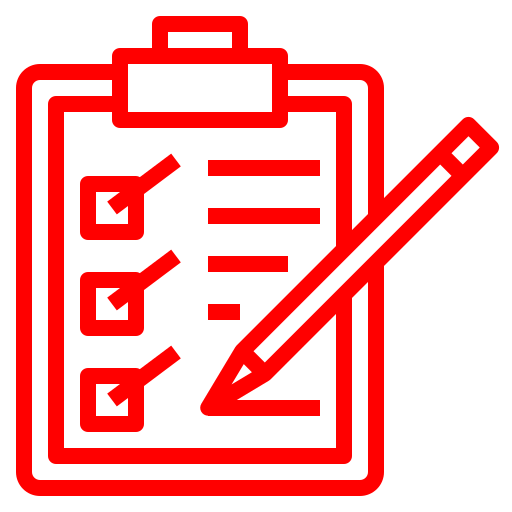
Dimensional inspection
check the casting dimension with precision toolings
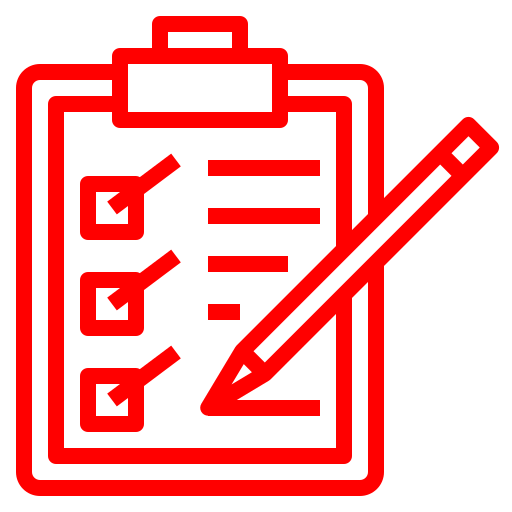
Hardness inspection
check casting surface hardness
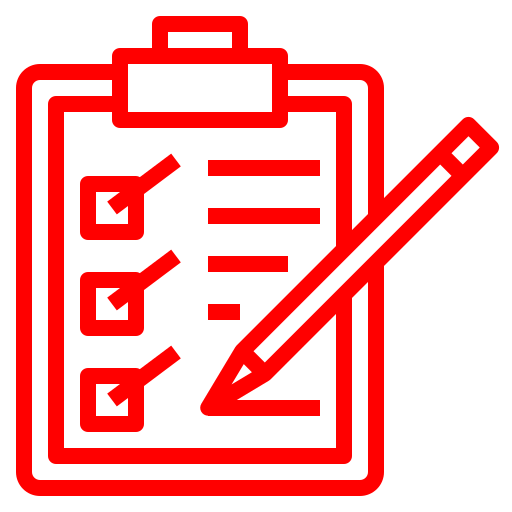
Liquid dye penetrant inspection
find tiny cracks, porosities, or other surface imperfections
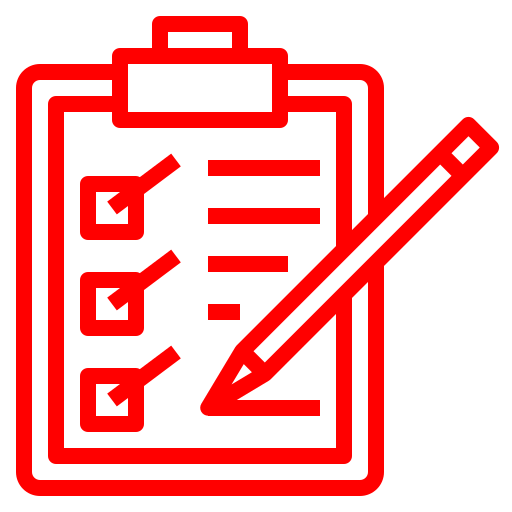
Ultrasonic testing
check for internal defects by using high-frequency acoustic energy transmitted into the casting
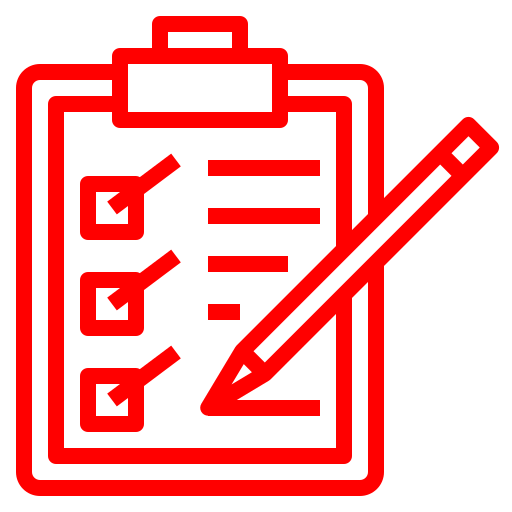
Spectrometer analysis
check the chemical composition of the casting
International Linkage
Integrating with international foundry technology & mastering new information in the global foundry industry
Year after year, we regularly visit various renowned international foundry exhibitions, intending to keep pace with the global foundry industry. We not only achieve innovation and breakthroughs in casting technology via these exhibitions but also derive significant benefits in the following four aspects:
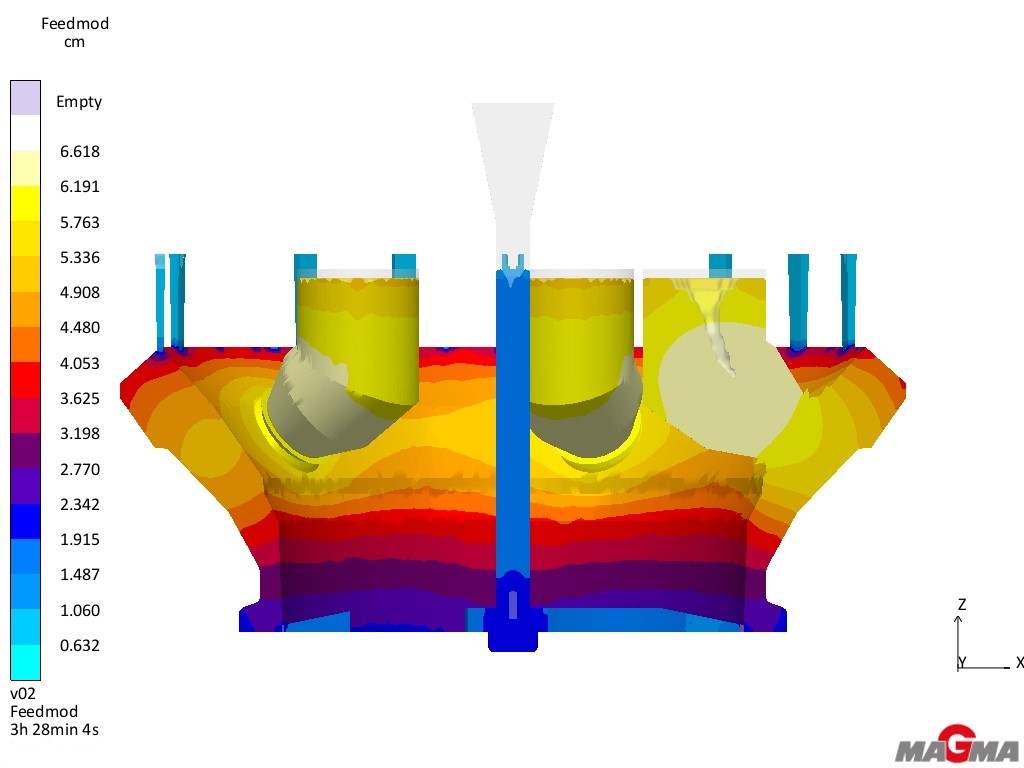
Understanding the latest trends and technologies
All these exhibitions bring together advanced technologies, equipment and innovative materials from the global foundry industry, enabling us to stay at the forefront of the latest developments and trends in the foundry industry.
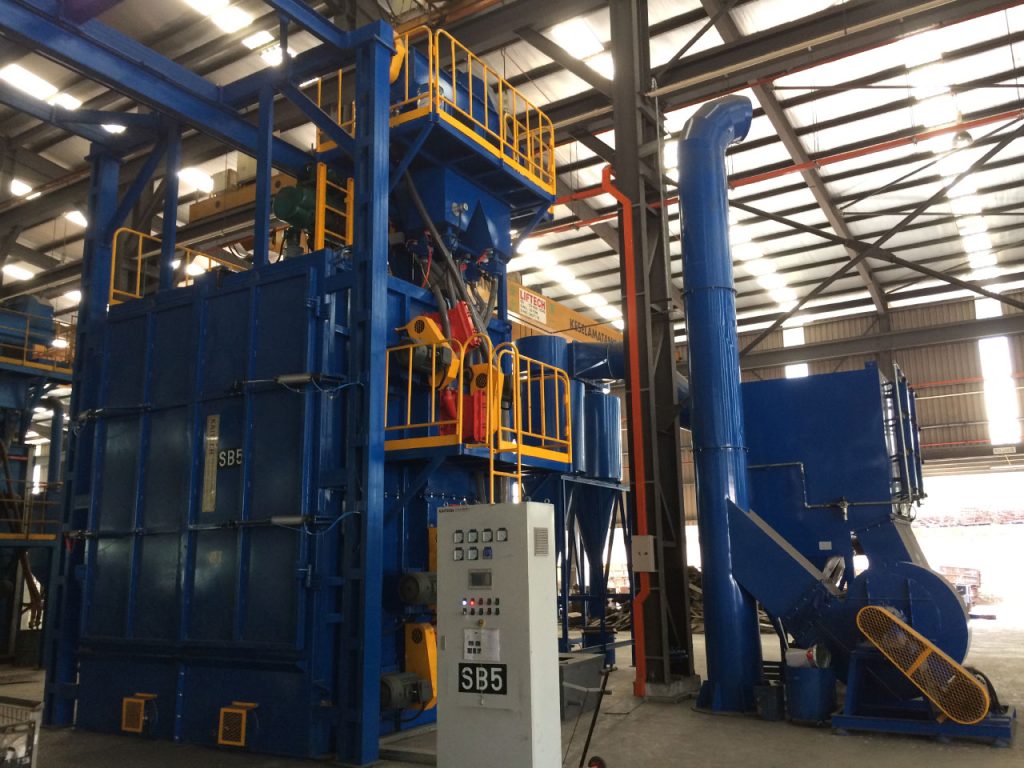
Study cutting-edge equipment & processes
Through on-site observation, we gain an in-depth understanding of advanced equipment and processes, allowing us to introduce cutting-edge technologies to further enhance production efficiency and casting quality.
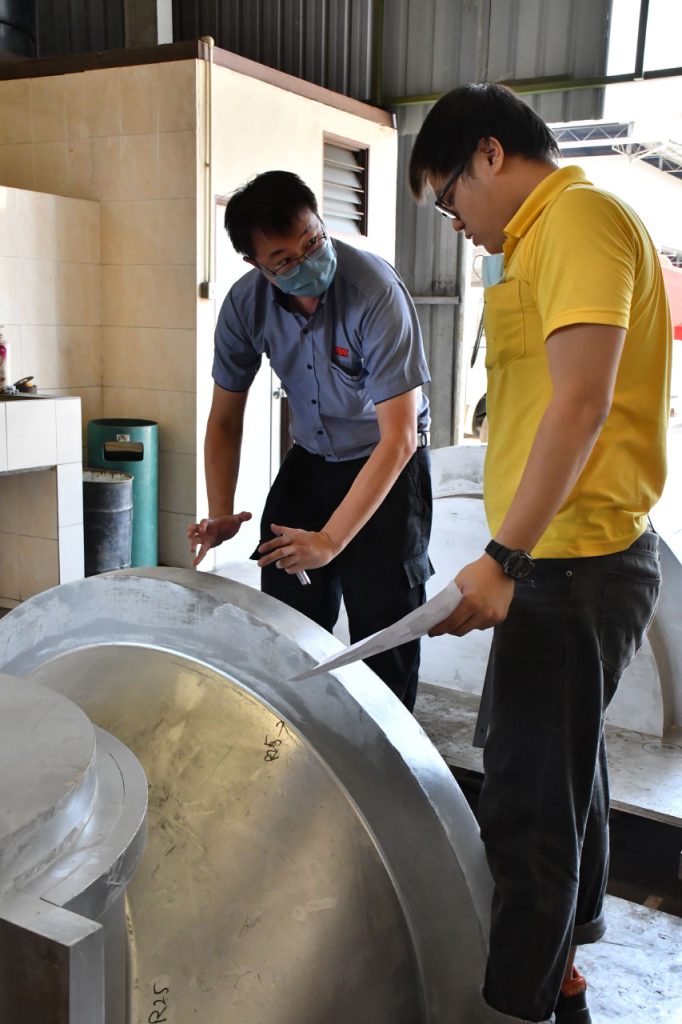
Seeking Partners
we have established close ties with other companies to seek out potential partners, such as equipment and material suppliers, technology partners, etc.
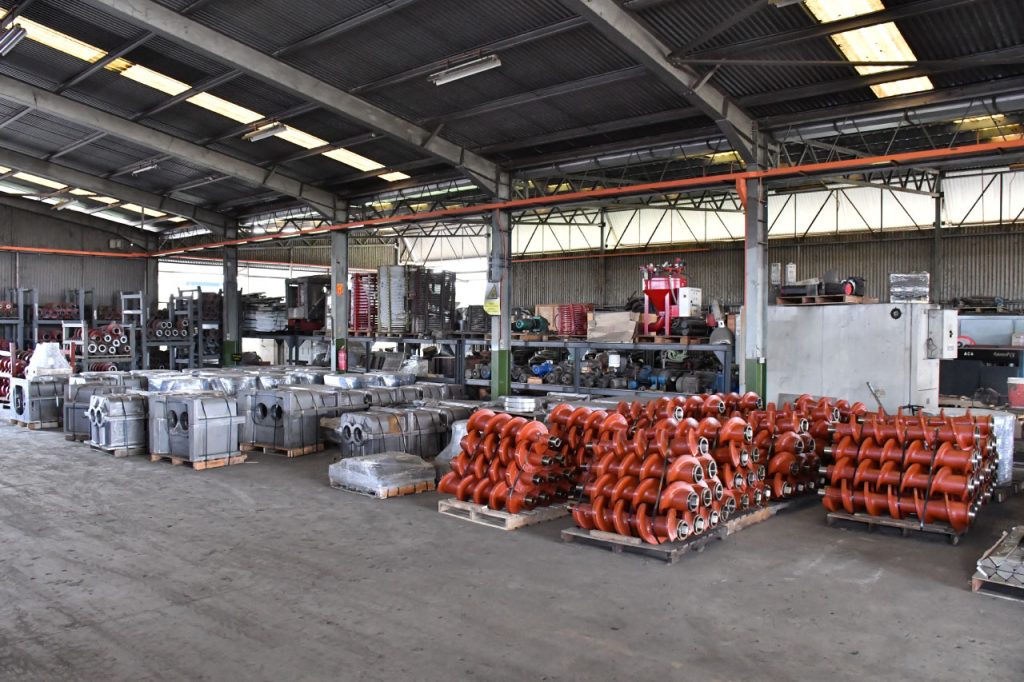
Understand customer needs
From these exhibitions, we gain a deeper insight into market demands to improve the quality of our customer service further.