Our Strengths
Satisfying Customer Demands for Quality and Quantity in Complex Casting Production
We proudly supply castings with a strong production capability supported by a bank of various sizes of melting furnaces. The average monthly productivity is 1,000 to 1,100 tons, while the production capacity can reach as high as 1,300 tons. In terms of casting production capacity, a single casting can weight up to 9 to 10 tons, while the smallest casting weighted 5 kilograms.
This allows us to meet project requirements of various scales and complexity, ensuring our customers receive satisfactory service in terms of quality and quantity.
Raw Materials
Utilizing Top-Quality Materials and Our Expertise to Manufacture Quality Castings
In the casting process, we use many different types of high-quality raw materials to create a variety of top-quality castings. These are the raw materials we use:
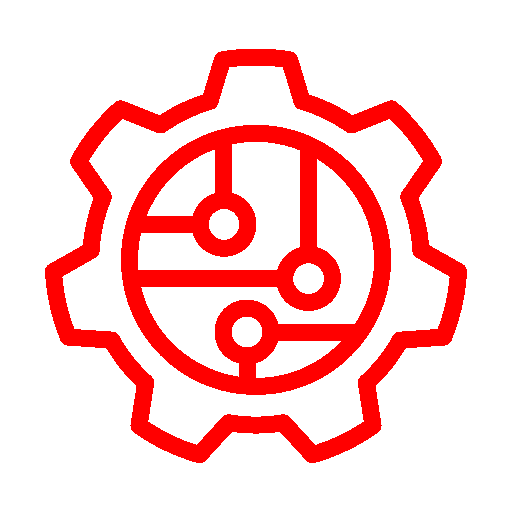
Top foundry grade scrap metal of various material specification
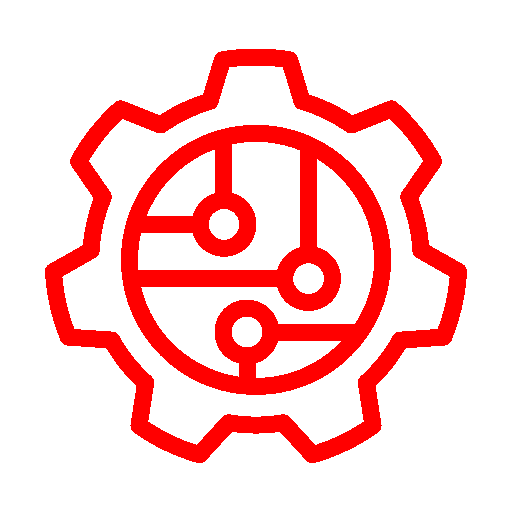
Quality moulding materials including various types of sand like Silica, Olivine and Chromite; exothermic sleeves and compounds; various types of refractory lining materials and coatings
Our craft involves the precise processing of these raw materials, and the selection of raw materials depends on actual product requirements to ensure that the final product has the desired quality.
Processing
Professional Processing Shapes Castings to Perfection
Although our castings are close to their final forms during the production process, we perform precision processing on them according to needs, including using a variety of advanced machinery, coupled with rigorous quality inspection standards, to give the castings the final perfect shapes. We perform the following types of processing work:
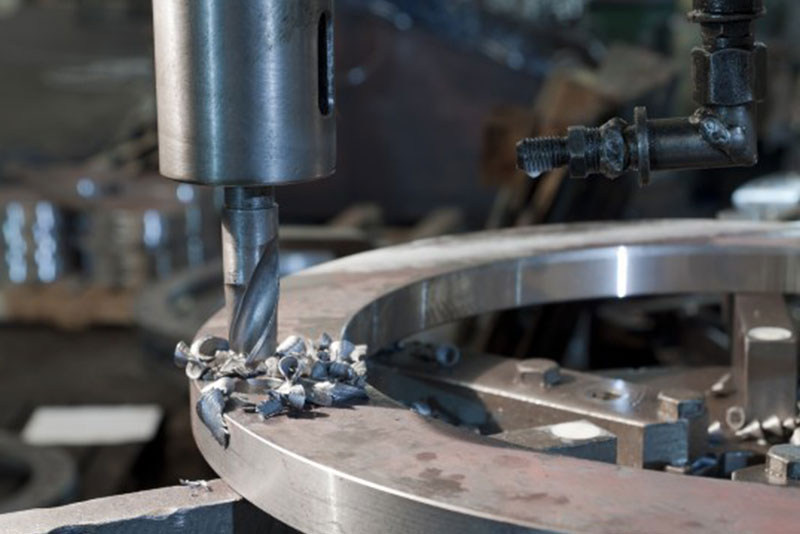
Drilling
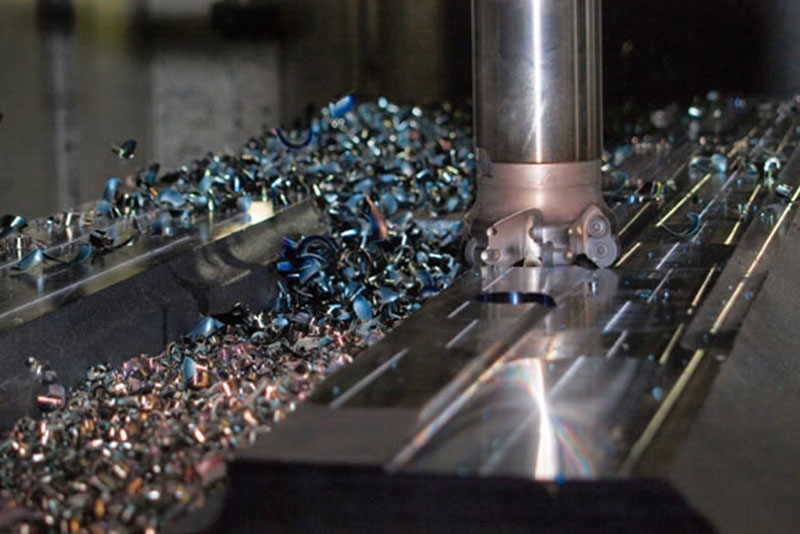
Milling
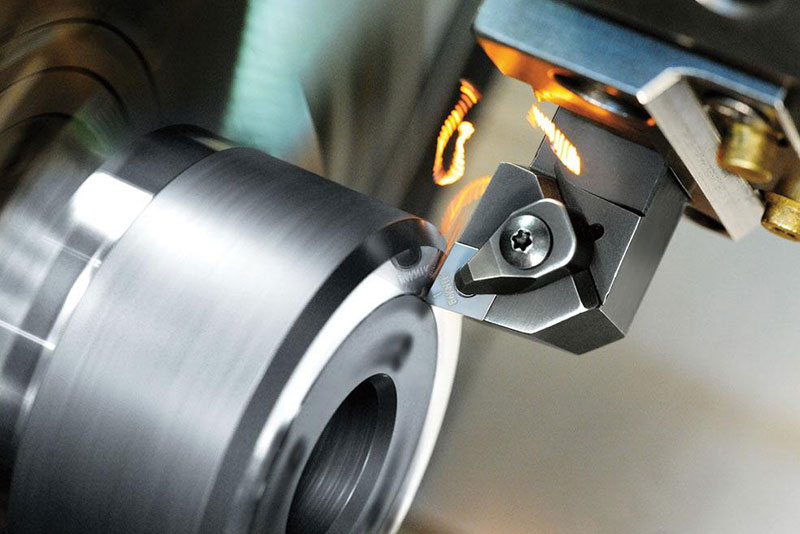
Turning
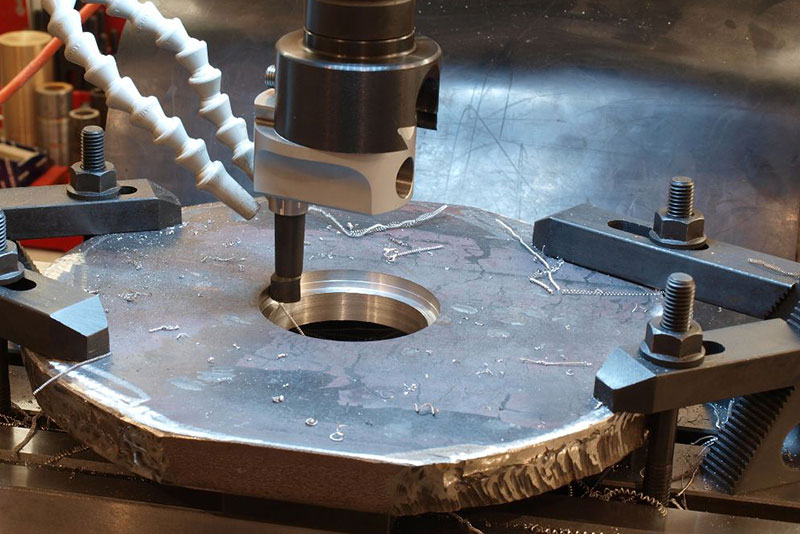
Boring
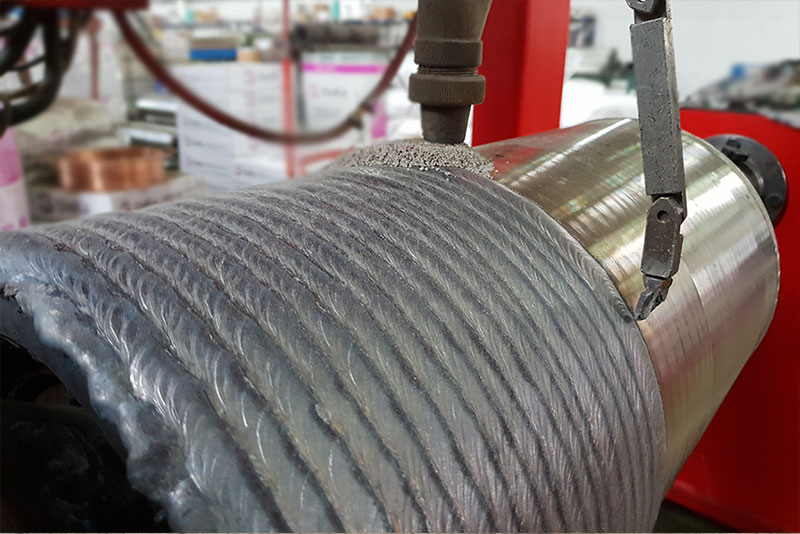
Hard Facing
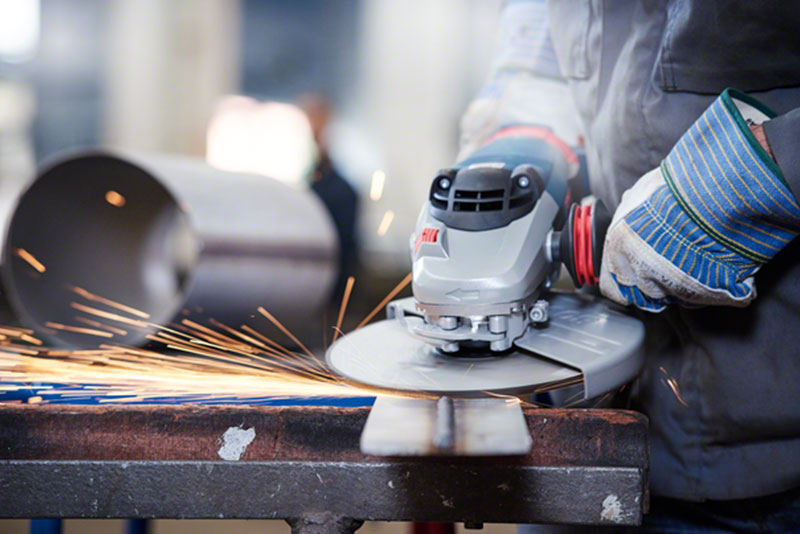
Grinding
Processing
Our Manufacturing Process: From Design to Perfect Molding
We follow a rigorous professional manufacturing procedure, which is carefully optimized to ensure efficient operation. Appended below is the production process flow: